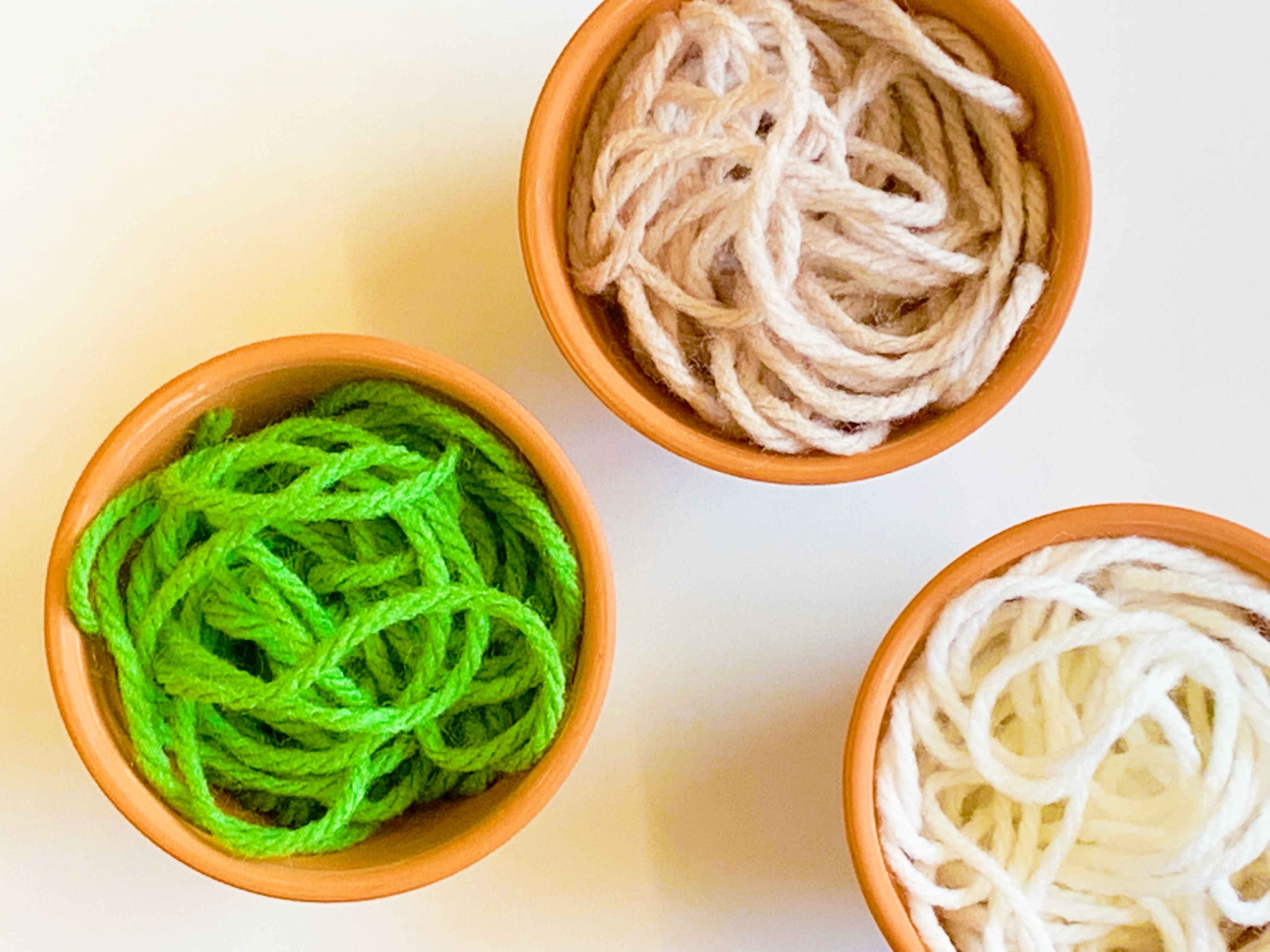
レーヨンからリサイクルポリエステル
素材だけでない、お客様が長く継続できる製品を目指して
最近では普通に生活していても、「サステナブル」という言葉を聞くことが多くなりました。
糸を販売しております私共にも、
「サステナブルな素材を提案してほしい」
「今使っている素材からサステナブルな素材に切り替えたい」
というご相談が数年前から増えています。
しかし、この「サステナブル」という言葉に、私は少し掴みがたい印象を持っています。
おそらくその言葉だけでは意味が広すぎるのです。
和訳すると「持続可能な」ですから、当然です。
その言葉を使うには、まずは「何を」を明らかにしなければなりません。
そしてその「何を」とは、SDGsに掲げられている17のゴールとは別に、ものづくりとして、会社として、継続可能であることを優先しなくては、悪く言えば「流行りに乗っただけ」、ただ開発費が増えるだけ、在庫が増えるだけ、面倒が増えるだけ、になってしまうことにもなりかねません。
先日、組紐をお取り扱いになられているお客様からご相談をいただきました。
「ユーザーさんから、うちの定番品をサステナブルな素材に切り替えてほしいと言われたけど、どうしたらいいだろう?」
そのお客様、その定番品にはこれまで数十年来、レーヨンをお使いになられています。
レーヨンの原料は木材パルプ、あるいはコットンリンター(綿花の種の産毛)です。
そのような天然由来の原料で作られた糸ですから、レーヨンは化学繊維ながら地面に埋めれば土に還ります。
ならば「バイオマス素材」あるいは「生分解性素材」としてサステナブルと言えますし、実際にそのような意図で使われているお客様もいらっしゃいます。
そこで「レーヨンもサステナブルな素材ですと、ユーザーさんにご説明すれば解決ではないですか?」と申し上げたところ、
「それは話したけど『今までと違うものがいい』んだって」と。
どことなく腑に落ちませんが、しかしよくある話でもあります。
そして、時代時代の流れに合わせて、新商品を開発しようという意欲は当然あるべきです。
この場合、代替素材の候補検討は意外と単純です。
お客様がなぜレーヨンを使われていたかと言えば、
「長繊維なので毛羽が立たず、光沢があって美しいから」です。
素材を切り替えた後もその特徴を残したいのであれば、コストも踏まえ、もはや選択肢は「リサイクルポリエステル」ということになります。
(リサイクルポリエステルの中でもその特徴に適ったものを選ばなくてはなりませんが)
しかし、そんなことはこのお客様もわかっているのです。
それでも「リサイクルポリエステル」に踏み切れないのは何故でしょうか?
それはご自身の会社にとって「まったくサステナブルではないから」です。
一番の理由は「在庫が増える」ということ。
いくらユーザーさんに「サステナブル」を求められたとしても、他には当然「レーヨンのままがいい」というユーザーさんもいるわけで、そうしたら用途の同じアイテムで2素材の在庫を持たなくてはなりません。
それによって売上が2倍になるならまだしも、2素材を構えたところですぐにユーザーさんが増えることも、用途が拡大することも期待はできません。
同じ売上で在庫だけが2倍。
私どもと同様に決して大きくない規模の会社さんにとって、その負荷は大きく、経営上は「サステナブル」とは言い難い状況になります。
とはいえ、当然ながら何もしないわけにも行きません。
大切なユーザー様のご要望ですし、きっとこの先もそのようなご要望が出てくることは容易に想像できます。
そうしたわけで色々お話をしておりましたところ、ポリエステルに素材を変えること自体は決して不都合なことばかりではなく、今よりも好都合なこともあると気が付きました。
・製品としての強度が増すこと
・堅牢度が向上すること(=色落ちしにくくなること)
・石油由来の素材は高熱で溶けるので、専用のヒートカッターで切れば、紐の切断面が解けにくくなること
などです。
そして、仮にレーヨンからリサイクルポリエステルへの完全移行を目指すとするなら、その移行期間では在庫が増えてしまうものの、決して2倍とまではならず、完全移行後にはやり方次第で今のレーヨンと比べて極端に在庫を圧縮できることにも気が付きました。
レーヨンの原糸を染色するとき、通常はケーク染色という染色方法を選びます。
しかし、ケーク染色はカセ染色やチーズ染色と比べてコストが低い反面、最低でも50kgの糸量がないと染色できません。
ですからこれまでは、毎日のように使っている色も、数ヶ月に1回しか使わない色も、同じ数量を補充しなくてはならなかったのです。
そこで、リサイクルポリエステルへの切り替えを目指すにあたっては、今までのレーヨンのように糸を染色してから紐に組むのではなく、まだ染色していないリサイクルポリエステルを紐に組んでから、紐の状態で染色することにしました。
(この製品の場合、レーヨンではそれが出来ない理由があるのですが、ここでは割愛します)
すると、ケーク染色以外の方法で染色できますから、最低でも50kgという制限がなくなりますので不相応な在庫負担が軽減できます。
また、既に紐に組んであるわけですから、度々依頼される別注色のご要望にも染色期間だけで対応でき、納期の大幅な短縮が可能です。
ユーザー様のご要望を叶え、品質が向上し、商売としての効率も上がる。
なかなかすべてが上手くいくことは難しいのですが、それでも「持続可能」というからには、誰かが我慢してそのツケを払わずに、それが社会にとっても経済にとっても価値のある製品になることが理想です。
ちなみに、リサイクルポリエステル製品の染色ですが、これまでレーヨンのケーク染色をお願いしていた工場さんではチーズ染色も可能なため、カセ染色ではなくチーズ染色でやることになりました。
当然ながら、その製品に携わる全社にとって「サステナブル」であることを目指したいと考えています。